Want to own a modular home? Find out the top things you should keep in mind when buying one!
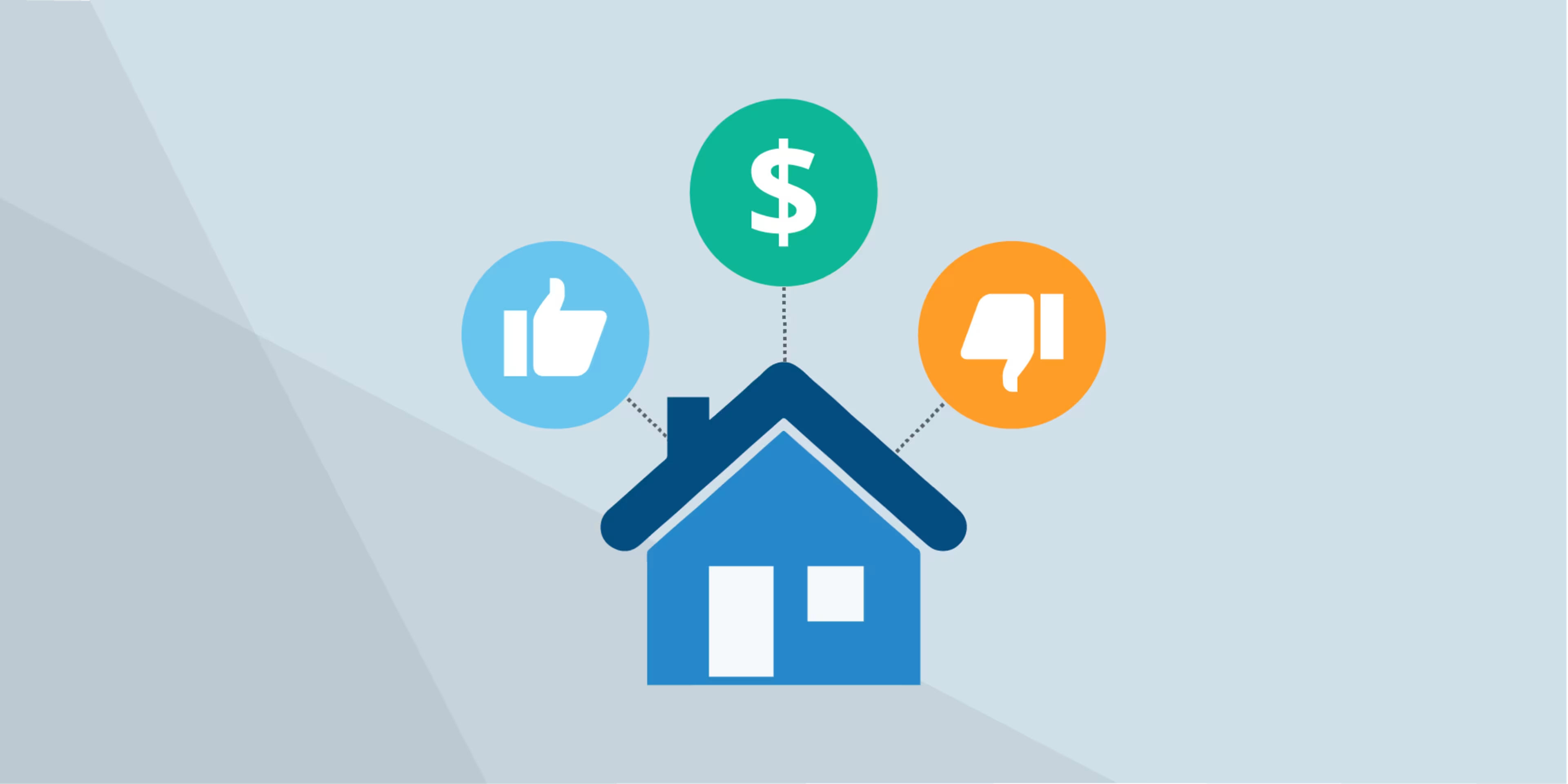
Buying a house costs a significant amount of money.
The median home price in the U.S. is around $245,000 as of this writing (via Zillow), so if you have to pony up 20% as a down payment, that's about $40,000 in cash you need up front.
Considering that 29% of households have less than $1,000 in savings, and the average savings account balance is $17,750, it's impressive how many people find a way into home ownership. But on the flip side, many are left out in the cold as a result of a financial barrier to entry.
Enter modular homes as a possible solution.
What is a modular home?
A modular home (also known as a prefabricated home) is entirely built in a factory, transported in parts, and assembled at the final construction site. The home looks like its traditional on-site developed counterparts but can be built and disassembled faster.
By purchasing a modular home instead of building one on-site, buyers can often get a new home sooner and cheaper. However, there are a few pros and cons you should consider before you decide whether modular is the way for you.
Pros and cons of modular homes
Pros
Portability: While modular buildings are generally built to be permanent structures, some designs can be disassembled so you can pick up and leave anytime you desire.
Quicker build: Since modular homes are built in a factory, unfavorable weather conditions don't delay construction. Also, much of the assembly is already done, which cuts down the building time for the final construction.
Lower cost: Using conventional construction methods can cost $150 to $250 per square foot if you're building a standard, non-luxury home. Modular construction can cost 10% to 20% less thanks to assembly line efficiency.
Cons
You can't customize as much: While you have some customization options with modular buildings, most designs come with limits on alteration.
You need to be near the factory: To keep cost and effort under control, buyers should try to purchase a modular home from the closest factory/company to them. Otherwise, you could end up paying for extensive transport costs.
Zoning is an obstacle: Modular buildings are relatively new to the construction industry, and local zoning boards are still catching up. You may run into some outdated zoning rules that could derail the project or even prevent you from building altogether.
3 key factors that determine the cost of modular homes
The cost of a modular home varies based on the U.S. state you live in, the type of home you want to design, and its size. Let's take a closer look at these three factors.
1. Location
Whenever you're talking about houses and real estate, this is your number one concern.
Where you build matters as much as what you build. A modular home in New York—where the median home value is a staggering $669,500—will cost substantially more than a home in West Virginia where the median home value is just $99,000.
There can also be additional costs based on the unique nature of your location, such as excavation costs, transportation costs, permit costs, land development, and sales tax.
How to factor this into your home cost:
Look up the median home price in your local market using Zillow's home values tool.
Calculate how your market compares to the national market as follows: Divide the current U.S. median home value by 100 ($231,700 as of November 2019, so the answer would be 2,317), then take your market's median home price and divide it into that figure.
If, for example, the answer is 80, that means your market is worth only 80% of the national market. If you got something like 133, your market is 33% more expensive than the national average.
2. Size
Once you've settled on a price per square foot, it's relatively easy to determine just how much you need to buy a house, based on its size. Here, it becomes simple arithmetic: You multiply the price per square foot by the square footage you're planning on.
The question is: How much square footage is going to be enough for you?
The average house size in the U.S. is 2,435 square feet, but do you need all that space? Or could you settle for less? Here's what a 1,300-square-foot house looks like.
How to factor this into your home cost:
Multiply the price per square foot you want with your desired square footage. Then, apply the modifier from the "Location" section.
For example, if you want 2,000 square feet at $150 per square foot, that will cost $300,000. If you live in a market that is 33% above the national median home price, you could end up paying about $400,000.
3. Design
The base price of some modular homes only cost $50 per square foot. If you multiply that by 2,435—the average square footage of U.S. homes—that's about $121,750 for a new home.
Having said that, the price climbs drastically depending on desired customizations. For example, utility hook-ups for electrical equipment and plumbing systems will incur additional costs. Likewise, further enhancements such as custom flooring and countertops will drive up your total cost of ownership.
And if you want luxury, it can cost upwards of $300,000 for the final product.
How to factor this into your home cost:
Factoring in customization costs depends on your unique requirements. The best way is to have clear, upfront conversations and agreements with the manufacturer about what customization you want and its total cost.
You can also use this helpful list to find your ideal design and get a rough estimate of how much it'll cost per square foot.
Want to learn more about modular construction?
Modular construction is a different concept, and there's sure to be some pitfalls for newcomers. Let us know about any obstacles you've come across in the comments below.
If you're trying to learn as much about modular construction as possible, try reading some of these other articles on the impact it's having on the construction industry:
8 Easy Ways to Improve Construction Efficiency on Your Project
How Modular Property Gives Your Business a Competitive Edge